Reliable PCBs for extreme conditions
How Wevo materials protect against electrocorrosion
When printed circuit boards are used in demanding applications, conventional conformal coatings are often not sufficient to protect against electrocorrosion. A proven electro potting resin from Wevo opens up new possibilities here, as a study by Denmark Technical University confirms.
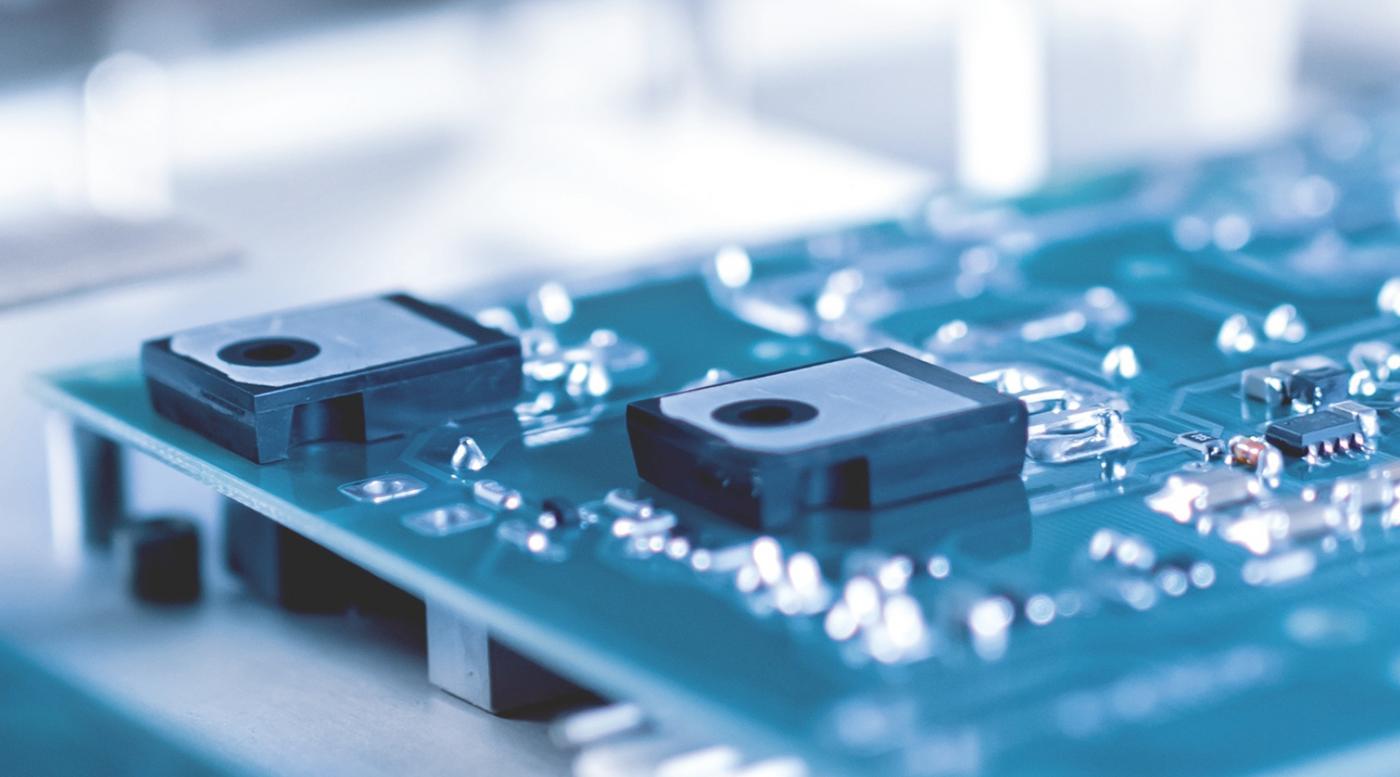
From e-mobility to renewable energies, printed circuit boards (PCBs) are a must in numerous cutting-edge technologies. The Printed Circuit Boards Group at the German Electro and Digital Industry Association (ZVEI) sums up some of the challenges arising: “The ongoing miniaturisation of electronic components and the increased demand for performance and speed require smaller and more densely packed PCBs to meet the increasing requirements. This development leads to an increased demand for high-speed PCBs and complex HDI multilayers.”
Furthermore, these increasingly sensitive components have to withstand extreme ambient conditions, for example in the battery management systems of electric vehicles or offshore wind turbines.
Electrocorrosion represents one of the biggest risks for PCBs. It occurs whenever moisture, impurities or chemical residues on the circuit board trigger an electrochemical reaction in conjunction with electrical voltage. This corrodes the metal conductors and could contribute to malfunctions or a drop in performance or cause the electronic components to fail completely in the long term.
Study framework
Effective protection of printed circuit boards from environmental influences is the focus of the Consortium for Climatically Reliable Electronics (CreCon). An industrial consortium under the umbrella of Denmark Technical University (DTU), not far from Copenhagen, CreCon brings industrial partners from various sectors together with scientists. The aim is to research innovative solutions for improving the corrosion resistance of electronic components.
In the context of Wevo being a member of CreCon the DTU conducted a study of special two-component potting compounds. The research was carried out as part of a doctoral thesis on measures to increase the reliability of printed circuit boards. DTU contributed expertise in electrochemical corrosion here while Wevo supported the work with extensive know-how about the formulation and processing of potting compounds.
The material under test: WEVOPUR 512 FLE
WEVOPUR 512 FLE, a two-component potting compound and a proven solution for modern electronic components, was chosen for the purpose of the study. From the product development stage onward, classic flame retardants such as phosphate compounds, which can favour electrochemical corrosion, were avoided. The risk of corrosion was further minimised by ensuring a low free ion content.
The polyurethane resin remains elastic when cured and is therefore mechanically very robust. The product can also be combined with various hardeners and, depending on the version selected, provides good-to-excellent adhesion to common substrates such as metals or plastics. WEVOPUR 512 FLE can additionally be processed with all standard, two-component mixing and dosing systems.
In view of these properties, the material is suitable not only for potting capacitors or fieldbus distributors but also for use with printed circuit boards.
Test specimens and procedure
The potting compound’s effectiveness as corrosion protection was established using surface impedance resistance (SIR) circuit boards with comb-shaped conductors (see graphic below). The number and spacing of these conductors determine the board’s electrical impedance, also referred to as the complex or alternating current resistance. Any changes to the surface – for example, due to corrosion – have a measurable effect on these values.
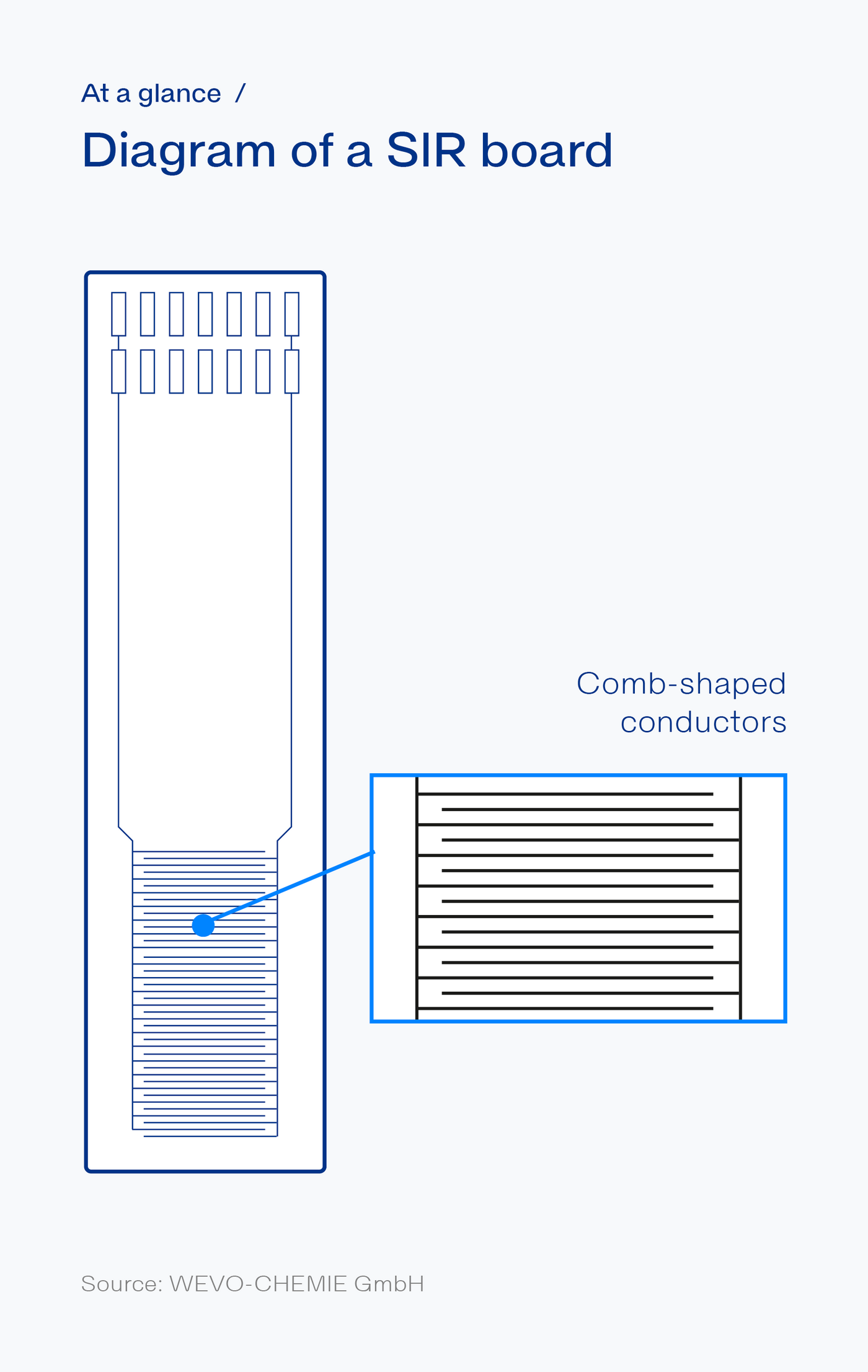
After being coated with WEVOPUR 512 FLE, the SIR boards were subjected to a predefined, cyclic climatic stress while measuring the electrical impedance. Corrosion – and especially the growth of dendritic structures on the circuit board – results in a drop in impedance here. It can also lead to so-called residual currents.
The cyclic climatic stress test entailed storing the coated SIR boards at a constant relative humidity, alternately for 2 hours at 40 °C and then for a further 2 hours at 65 °C – with a total of 20 consecutive cycles. The change from 65 to 40 °C accelerates the condensation of water vapour. This can favour the formation of dendrites when voltage is applied. To speed up this process, the boards were energised with 25 mV AC during the cyclic climatic stress test.
Results: Influence of contamination
The procedure described here was carried out in the first test phase using pre-cleaned SIR boards, either with WEVOPUR 512 FLE or with a conformal coating based on acrylic, acrylic-modified urethane or silicone. The impedance of the SIR boards at the start of the study was approximately 108 ohms. Merely minor changes were observed when the boards were subjected to cyclic climatic stress. Only the acrylic-based conformal coating performed worse, with a drop of the impedance to approximately 2⋅106 ohms (see graphic below, “Pre-cleaned”).

However, since contamination is commonplace in PCB manufacturing – for instance, owing to flux residues or fingerprints brought about by improper handling – the second test phase was conducted using contaminated SIR boards. Such impurities can be highly conducive to the development of electrochemical corrosion.
The amount of contamination was selected based on a general impurity concentration limit of 1.56 µg/cm², calculated previously by DTU, below which a PCB is regarded as clean. In addition to this, a flux that also favours electrochemical corrosion below this concentration limit has already been identified in another CreCon project. This flux was used as a contaminant at a concentration of 1.56 µg/cm². Cyclic climatic stress tests were subsequently carried out on all SIR boards.
The results are shown in the graphic above (“Flux contamination”). Differences in the impedance drop were likewise observed for the conformal coatings that were tested in this way: in the case of the acrylic-based coating, the impedance went down to 4⋅105 ohms, whereas with the acrylic-modified urethane-based coating it dropped to 7⋅104 ohms. The silicone-based coating showed the worst performance with less than 4⋅103 ohms. By contrast, WEVOPUR 512 FLE – with 6.5⋅107 ohms on the contaminated PCB – performed practically as well as on a clean PCB (5⋅107 ohms).
More tests were carried out with NaCl contamination. Previous studies by the CreCon consortium have demonstrated that contamination of this kind increases the risk of electrochemical corrosion, even if the circuit boards are coated. Once again, WEVOPUR 512 FLE proved very effective and there was no deterioration in performance.
Results: Immersion in water
The next stress test involved immersing the contaminated (flux and NaCl) SIR boards coated with Wevo material in deionised water (DI water). They were then energised with 5 V DC (direct current) for one hour a day over a 40-day period. The residual current was monitored at the same time – an increase to more than 0.1 mA was considered to be evidence of incipient electrical corrosion and as such an exclusion criterion for the circuit board. The results (see graphic below) confirm that the residual current was well below the limit for all PCBs throughout.
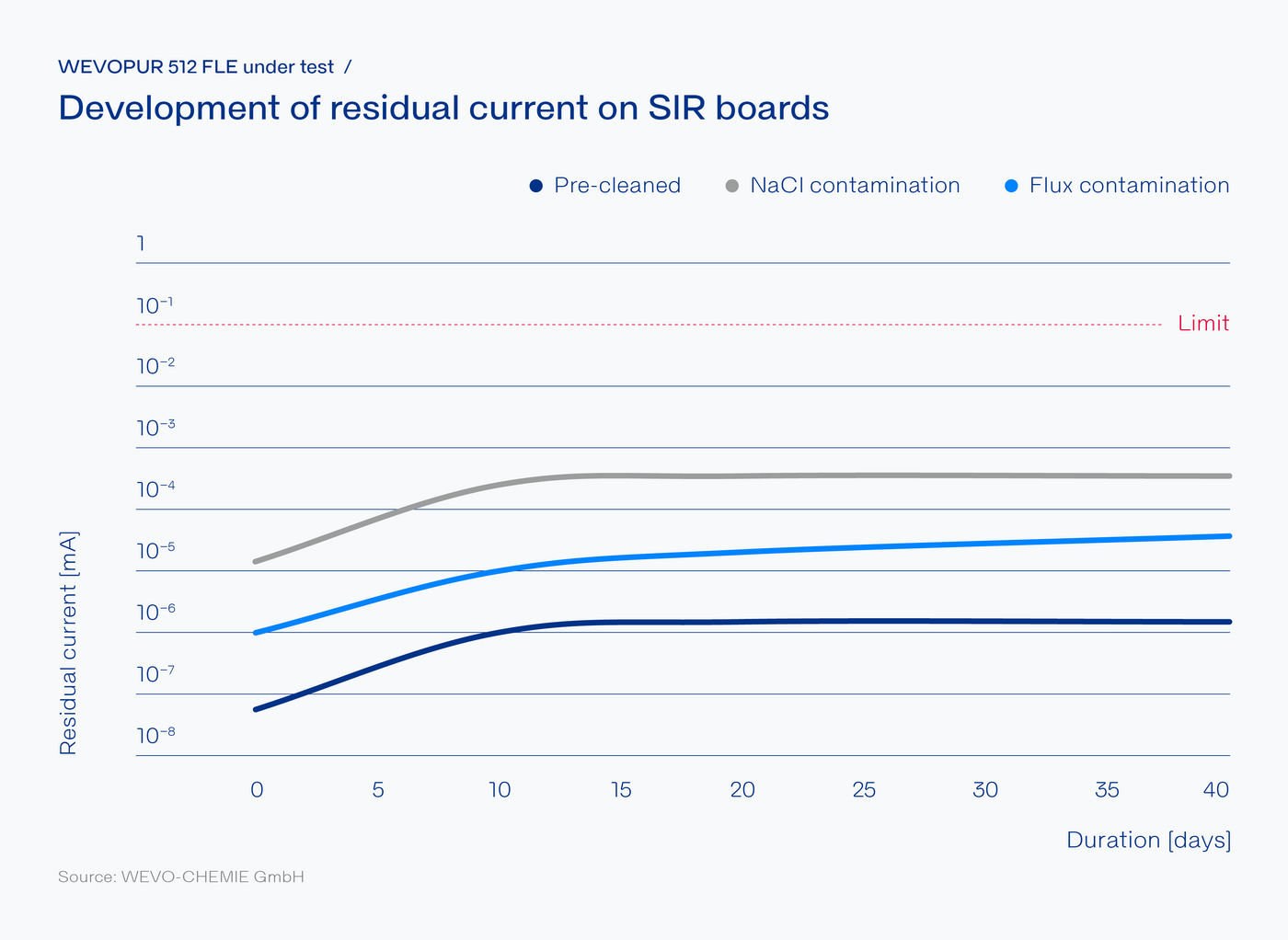
Results: Adhesion of the protective coating
Adhesion was likewise analysed as a factor influencing corrosion protection. Assumption: The lower the adhesion of a protective coating, the easier it is for moisture to penetrate to the circuit board and form a water film there that favours electrocorrosion.
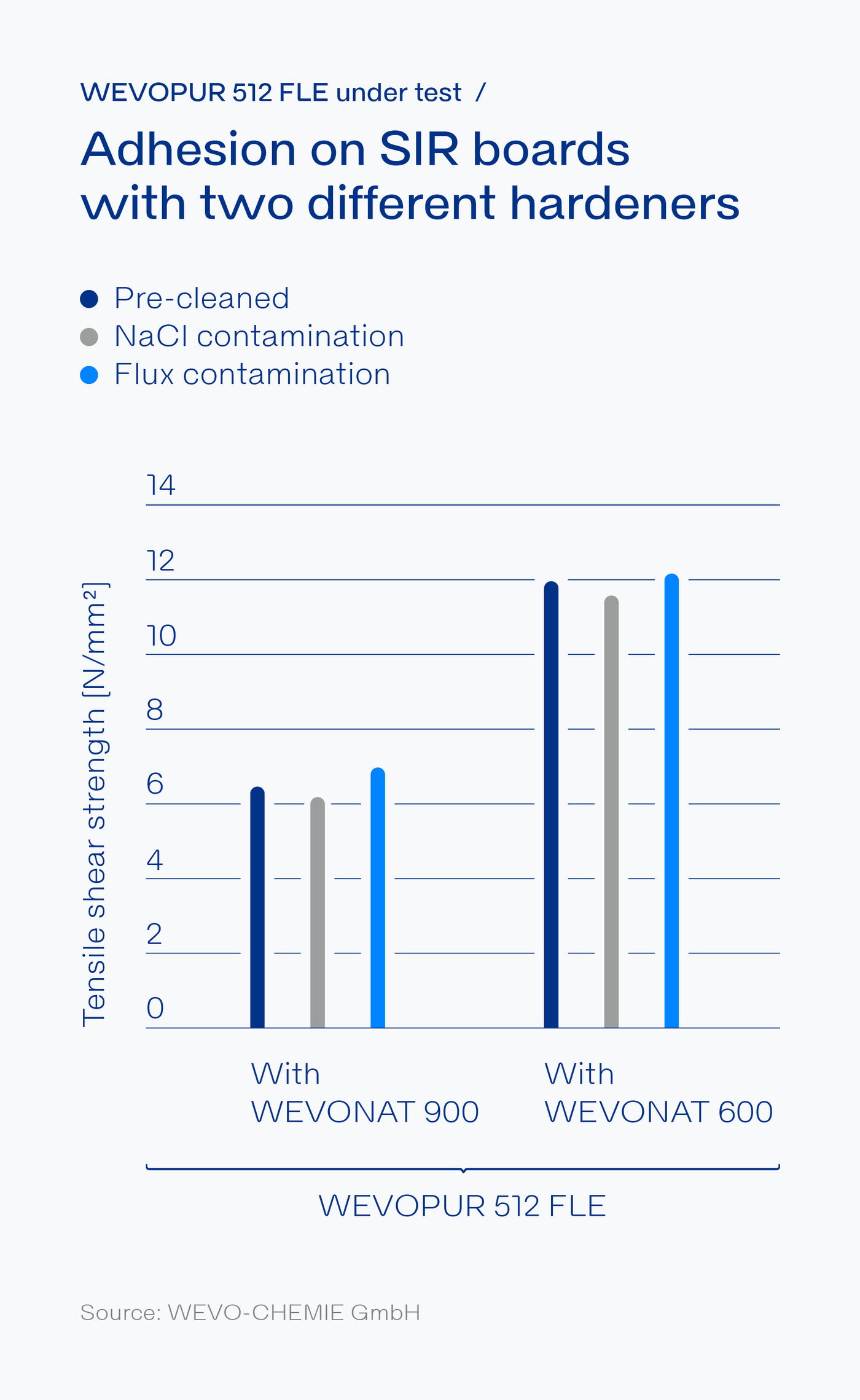
To verify this correlation, WEVOPUR 512 FLE was tested with two different hardeners: the standard WEVONAT 900, which was also used for the previous tests, and WEVONAT 600, a special-purpose hardener with optimised adhesion. The graphic on the left illustrates the positive effect: WEVONAT 600 doubles the tensile shear strength of WEVOPUR 512 FLE to 12 N/mm².
The measurements moreover confirm that neither flux nor NaCl contamination (concentration: 1.56 µg/cm² in each case) has any significant effect on adhesion for all SIR boards coated with Wevo material.
In a further test to determine the long-term resistance of the potting compounds, the coated SIR boards were immersed in salt water for 100 days and energised with 5 V DC for one hour every day. The results show that the SIR boards with a combination of WEVOPUR 512 FLE and WEVONAT 600 were still fully functional after immersion. By comparison, the boards coated with WEVOPUR 512 FLE and WEVONAT 900 started to fail after around 75 days. Optimised adhesion is thus clearly crucial for long-term protection against electrochemical corrosion.
Summary and outlook
The study carried out under the umbrella of the CreCon consortium confirms that WEVOPUR 512 FLE is highly effective as protection against electrochemical corrosion on printed circuit boards. Whereas on pre-cleaned PCBs, the material has a similar protective effect to conventional conformal coatings, it offers clear advantages in the presence of contamination, for example due to flux or NaCl. First and foremost, it provides a decidedly more reliable barrier against corrosion. Resistance under extreme ambient conditions can likewise be greatly improved by using the Wevo potting compound.
What’s more, the resin offers flame-retardant properties in accordance with UL 94 V 0 and is suitable even for critical environments such as passenger trains. EN 45545 2, the European railway standard, sets out strict rules here regarding fire behaviour and smoke development, which are fulfilled by the material. In short, WEVOPUR 512 FLE is a reliable solution for numerous high-tech applications where durability and resistance under demanding ambient conditions are a top priority.
Image source: YouraPechkin (stock.adobe.com)
Links related to this article
Disclaimer (Extract) – Copyright and IP Rights: The contents published on this website are subject to German copyright and ancillary copyright law. Any utilization not permitted by German copyright and ancillary copyright law requires the prior written permission by the provider or the respective owner. This applies in particular to the copying, working, translation, storage, processing and reproduction of contents in databases and other electronic media and systems. Third-party contents and rights are identified as such in this regard. The unauthorised duplication and forwarding of individual contents or complete pages is not permitted and may possibly be punishable as a criminal offence. Only the creation of copies and downloads for personal and private and non-commercial use is permitted. The use of this website as external link shall only be permitted upon prior written approval oft he provider. Each and any firm or trademark is sole property of the relevant company. Citations of trademarks and names of third parties have a purely informative character. You will find the complete disclaimer in the imprint.